Products
Accessories
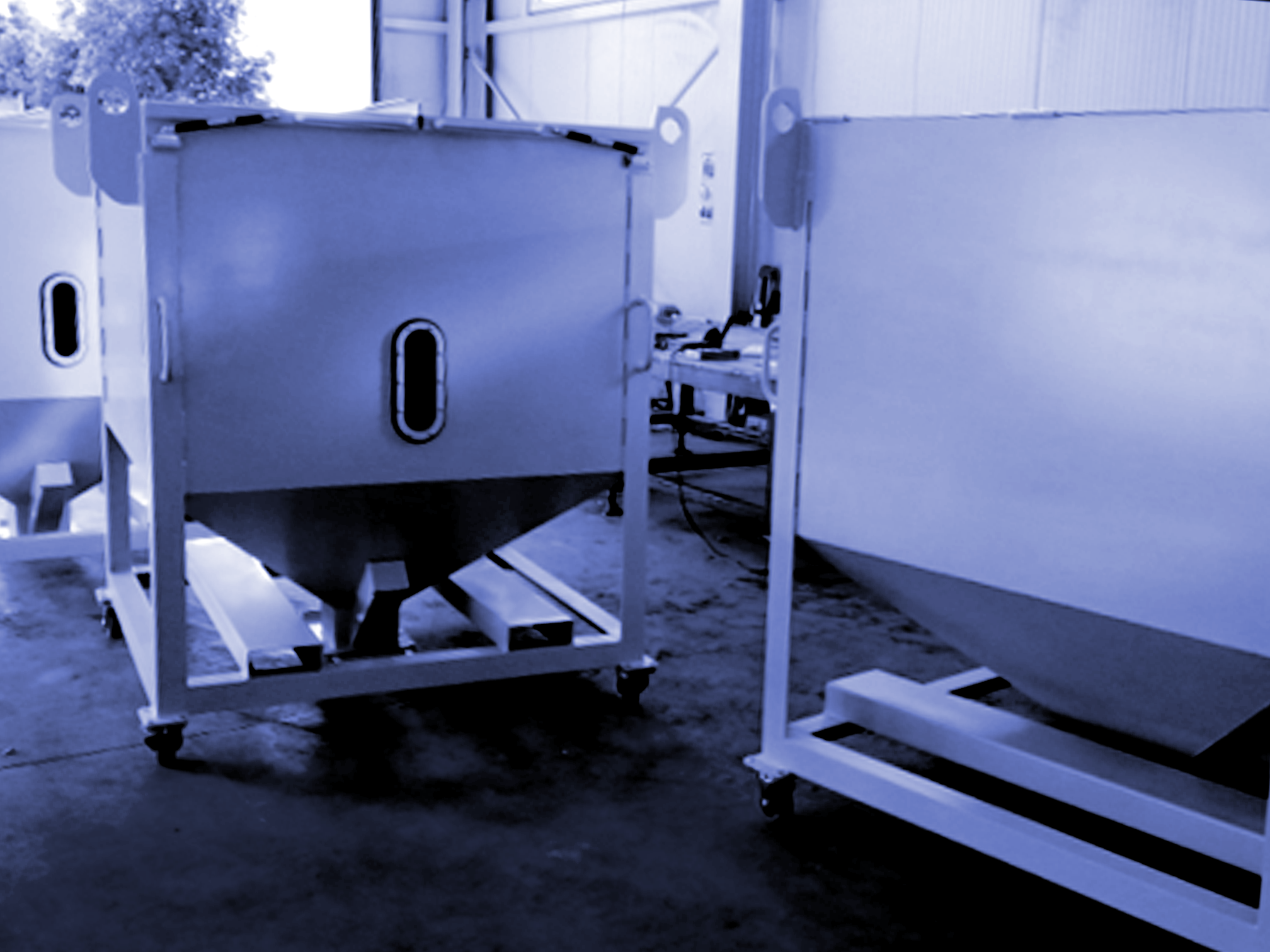
Material feeding system
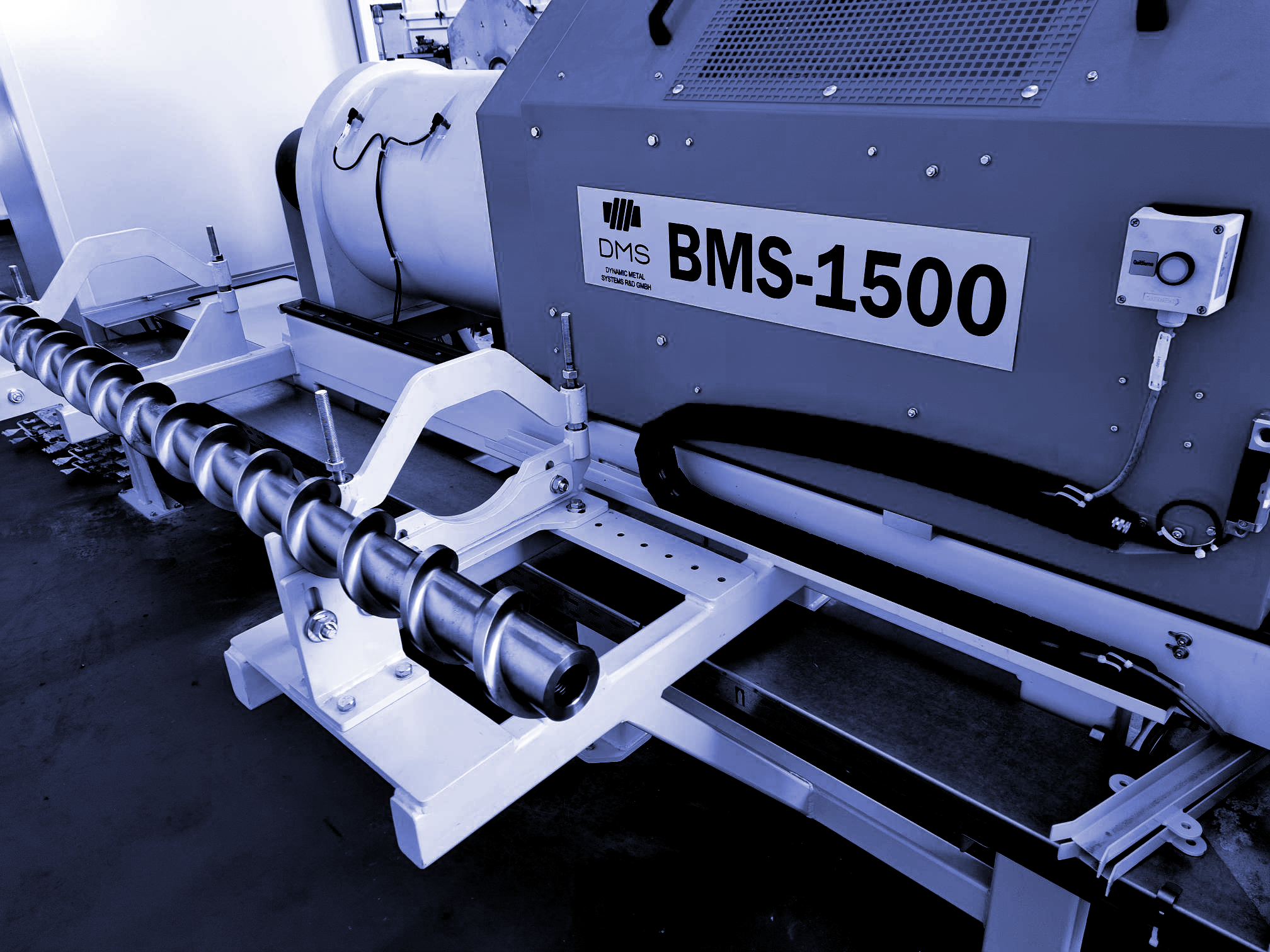
Injection unit maintenance station
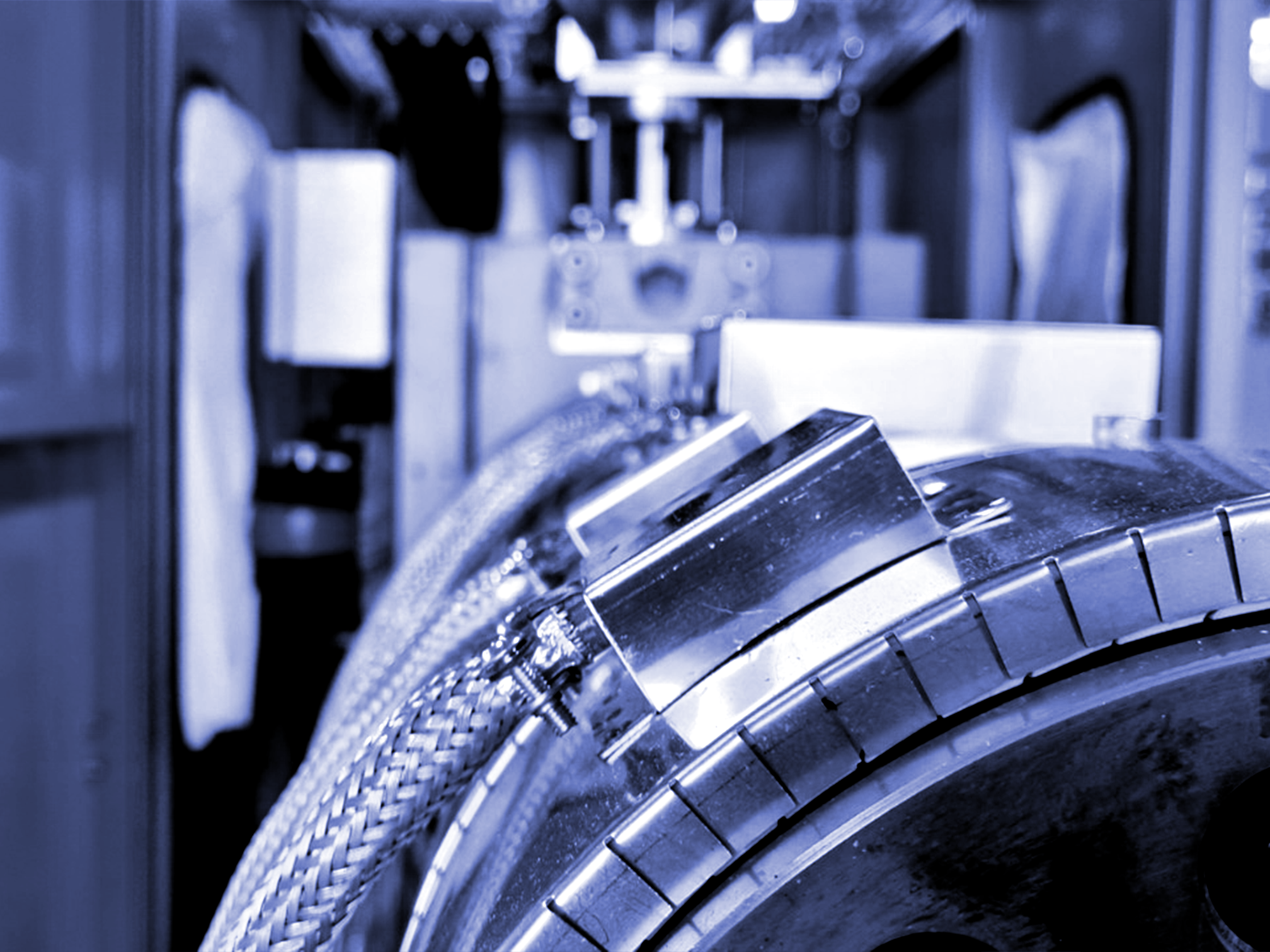
Customized spare parts
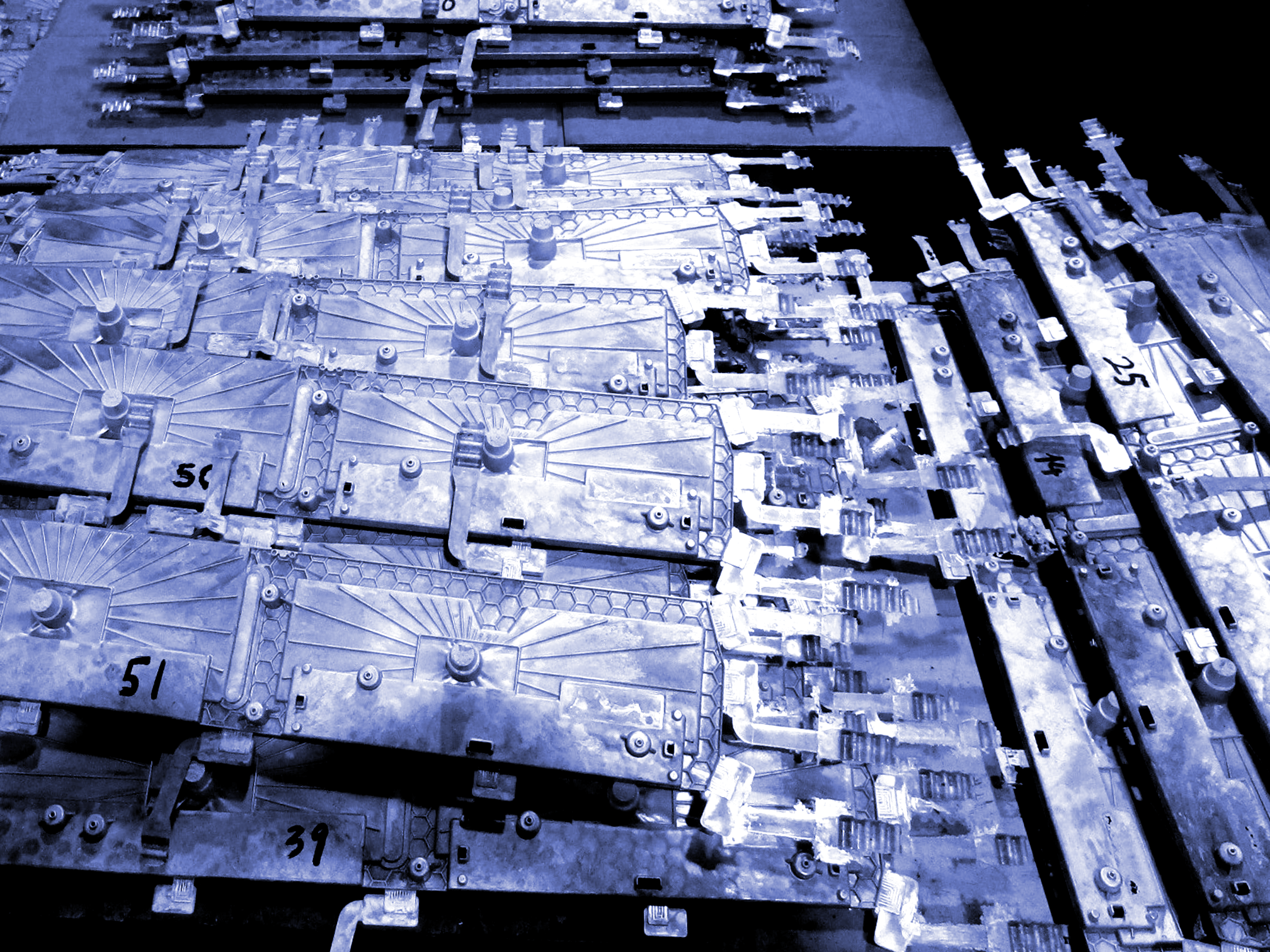
Multi-gate Hotrunner
TPI vs. Die Casting
Energy Efficiency
TPI offers a remarkable reduction in energy consumption of up to 50% compared to conventional cold chamber die-casting. This is achieved through various factors, including significantly lower operating temperatures (approximately 100°C lower), reduced magnesium consumption for product manufacturing (thanks to reduced runner sizes through nozzle technology), and the high dynamic potential of the system, allowing for rapid cylinder cooling over the weekend and a quick restart within 1-2 hours.
IMPROVED WORKER SAFETY
TPI uses only a minimal amount of high-temperature magnesium, approximately 2-3 times the amount of the shot size, as the melt is produced just in time. In contrast, dosing furnaces contain significantly larger quantities of magnesium.
REDUCED MATERIAL CONSUMPTION
The use of nozzles in TPI for the direct introduction of magnesium into the cavities significantly reduces the need for runners to distribute magnesium from the casting channel to the workpiece.
COST OF OWNERSHIP
Extended tool lifespan, longer spare parts life, savings on casting materials, reduced energy consumption, and shortened cycle times are crucial features contributing to cost reduction in TPI production.
ENVIRONMENTAL RESPONSIBILITY
TPI relies solely on electrical energy and avoids the use of protective gases and gas for melting alloys, contributing to a more environmentally friendly manufacturing process.
IMPROVED PRODUCT QUALITY
Semi-liquid casting processes offer a 20% increase in component durability, noticeable through higher elongation and tensile strength due to a finer microstructure and lower porosity.
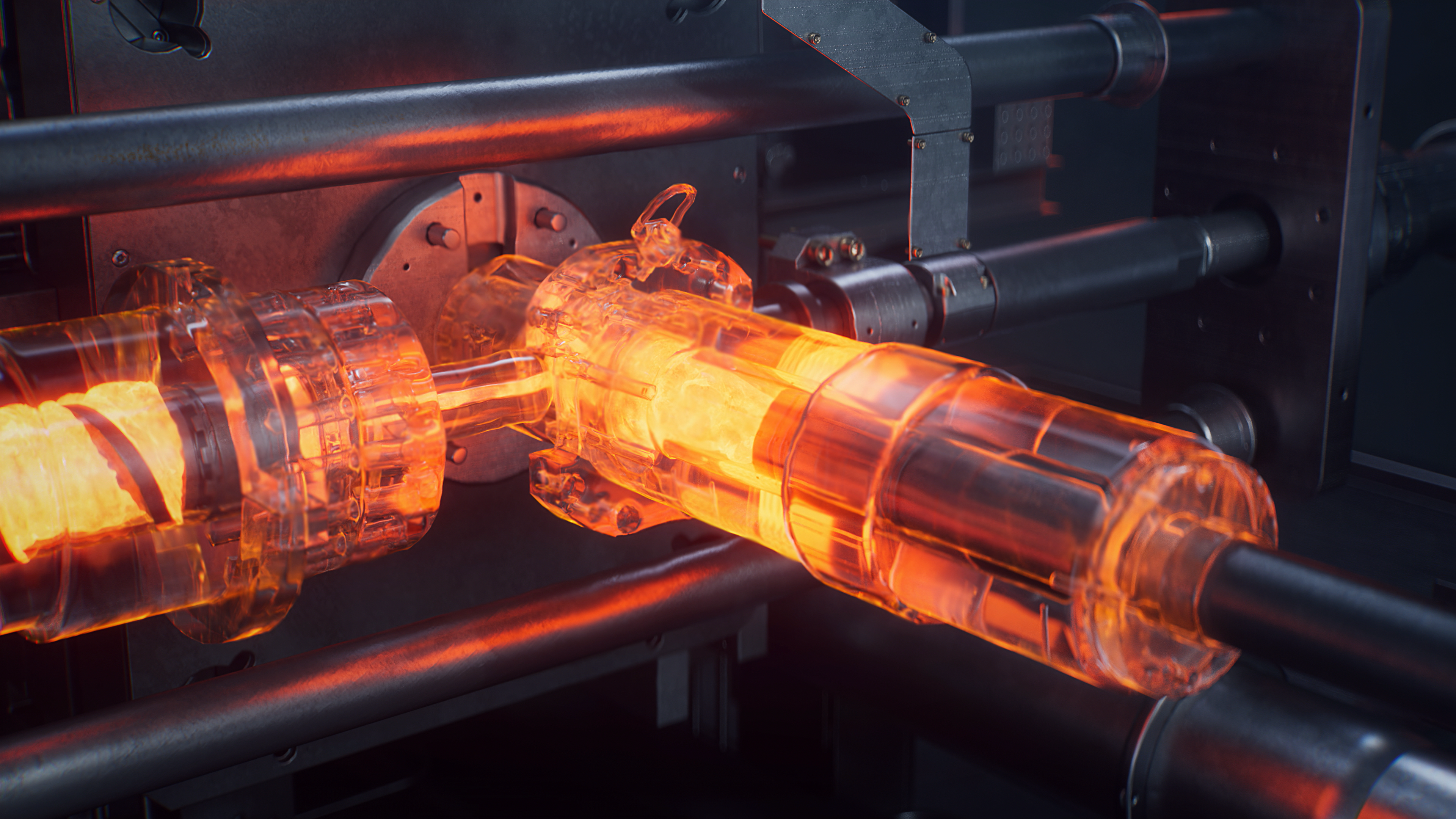
TPI vs. Thixomolding
Melting performance
To achieve the required melting rate and cycle times for larger products or alloys like AM50, larger diameter and longer screw assemblies can be used. TPI allows for maintaining the needed shot dynamics, as there is no need to accelerate the heavy screw during injection
HOLDING PRESSURE
Thixomolding machines do not offer the ability to build holding pressure from accumulators and multipliers; instead, they exclusively use oil from the hydraulic pump for this purpose.
NO CHECK VALVE
In Thixomolding, the presence of a check valve is crucial to ensure product quality. However, maintaining the check valve is typically labor-intensive and costly. Its function is also dependent on friction factors and dynamics. In TPI, the dosing chamber is sealed from the filling chamber through hydraulic, precisely controllable movements.
MACHINE DYNAMICS
Compared to Thixomolding machines, die-casting machines have a significantly broader performance range (PQ² and nomogram).
AVAILABILITY
The components used in TPI are readily available standard components worldwide, including brands like Siemens, Bosch Rexroth, and SEW.
MATURED MACHINE BASE
TPI machines offer several advantages, including retractable tie bars, compact machine lengths, high closing forces, and the flexibility to cast aluminum when needed.